Efficiency-Increasing Strategies for Industrial Press Systems
페이지 정보
작성자 Alissa Cowper 작성일25-04-01 16:26 조회4회 댓글0건관련링크
본문
Regarding it comes to industrial filtration operations, money saving can be achieved through a combination of operational efficiency. The filtration device is a important piece of tool in different industrial processes, including mining.
For most situations, filter presses account for a significant portion of a factory's operating costs. The costs associated with wastewater treatment operations comprise electricity, workforce, maintenance and additional resources like substances and raw materials.
Some manufacturers and operators are now leveraging cost-saving strategies to minimize these expenses and boost their benefit.
One cost-saving strategy for filter press operations is minimizing cake removal. Filter cake is the solid material that stays after the filtration process is complete. Handling cake efficiently involves regulating the moisture levels within the cake and minimizing the pressure needed to remove the cake from the filter plates.
Strategies such as pre-treatment, cake management, and drying systems can all be used to attain this goal.
For addition to optimizing cake management, using a robust maintenance routine is also a vital factor in cost savings. Routine repair supports avoid costly repairs, increases the lifespan of the tool, and ensures that it operates at highest levels.
That includes carrying out scheduled inspections, replacing frayed parts, and educating operators to carry out maintenance tasks efficiently.
Another area to prioritize on is energy efficiency. Rising numbers of manufacturers and operators are improving eco-friendly technologies and systems, which assists to reduce power consumption and minimize costs.
The includes using variable-speed drives, LED lighting, and optimized control systems. In combination with the adoption of more power-saving equipment, the implementation of a complete energy-saving strategy can lead to substantial cost reductions.
The use of advanced monitoring and control systems is also a cost-saving strategy that is rapidly taking traction in the field. Such advanced monitoring systems allow operators to track vital performance indicators, identify areas for enhancement, and make data-driven decisions.
The resulting data can permit more effective operations, maintenance and planning.
As it comes to goods and substances, cost savings can be achieved through the implementation of eco-friendly practices and cost-reducing technologies. One option for achieving this includes implementing advanced filtration technologies that minimize the amount of chemicals required. Additionally, investing in eco-friendly and reusing waste-based technologies can also lead to significant cost savings.
For several manufacturers and operators, the way to cost-saving strategies begins by participating with expert professionals. Manufacturers and operators are increasingly seeking the inputs of skilled engineers and consultants to gain important insight into optimized oil filter manufacturing machine press processes. This not only saves capital and costs but also enables companies to achieve sustainability while reducing garbage and carbon footprint.
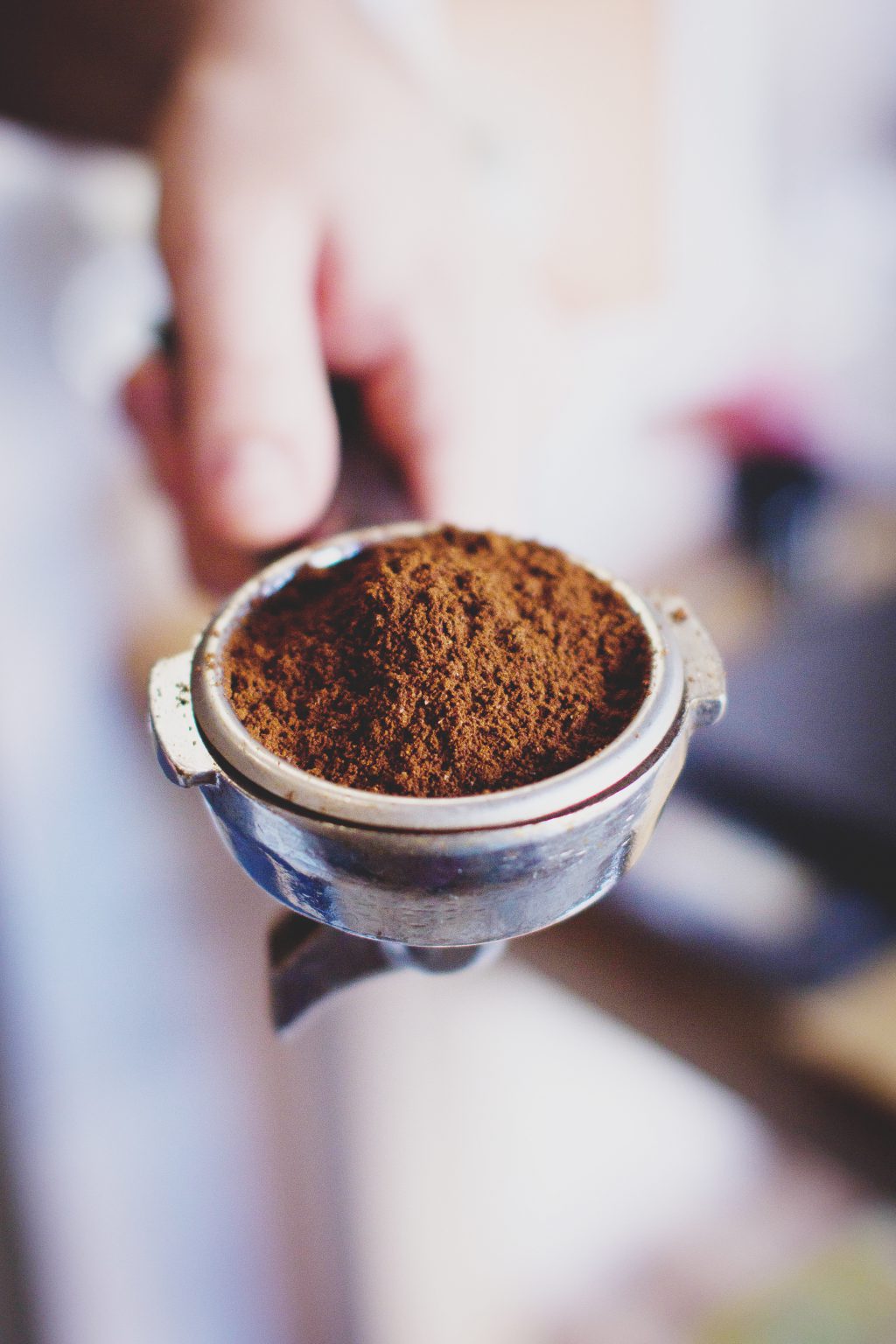
Some manufacturers and operators are now leveraging cost-saving strategies to minimize these expenses and boost their benefit.
One cost-saving strategy for filter press operations is minimizing cake removal. Filter cake is the solid material that stays after the filtration process is complete. Handling cake efficiently involves regulating the moisture levels within the cake and minimizing the pressure needed to remove the cake from the filter plates.
Strategies such as pre-treatment, cake management, and drying systems can all be used to attain this goal.
For addition to optimizing cake management, using a robust maintenance routine is also a vital factor in cost savings. Routine repair supports avoid costly repairs, increases the lifespan of the tool, and ensures that it operates at highest levels.
That includes carrying out scheduled inspections, replacing frayed parts, and educating operators to carry out maintenance tasks efficiently.
Another area to prioritize on is energy efficiency. Rising numbers of manufacturers and operators are improving eco-friendly technologies and systems, which assists to reduce power consumption and minimize costs.
The includes using variable-speed drives, LED lighting, and optimized control systems. In combination with the adoption of more power-saving equipment, the implementation of a complete energy-saving strategy can lead to substantial cost reductions.
The use of advanced monitoring and control systems is also a cost-saving strategy that is rapidly taking traction in the field. Such advanced monitoring systems allow operators to track vital performance indicators, identify areas for enhancement, and make data-driven decisions.
The resulting data can permit more effective operations, maintenance and planning.
As it comes to goods and substances, cost savings can be achieved through the implementation of eco-friendly practices and cost-reducing technologies. One option for achieving this includes implementing advanced filtration technologies that minimize the amount of chemicals required. Additionally, investing in eco-friendly and reusing waste-based technologies can also lead to significant cost savings.
For several manufacturers and operators, the way to cost-saving strategies begins by participating with expert professionals. Manufacturers and operators are increasingly seeking the inputs of skilled engineers and consultants to gain important insight into optimized oil filter manufacturing machine press processes. This not only saves capital and costs but also enables companies to achieve sustainability while reducing garbage and carbon footprint.
댓글목록
등록된 댓글이 없습니다.