Explaining Press Phases and Cycle
페이지 정보
작성자 Tracy Spaull 작성일25-04-01 01:59 조회18회 댓글0건관련링크
본문
The Press are a commonly used machine for sectors including waste treatment, wastewater processing, or industrial processing for separate solid-liquid mixtures. This process requires passing a suspension of solids in a liquid via a medium material, resulting to a solid formation of formed and the liquid is released as waste.
The procedure of the Filter can be divided into four primary phases: Blow, Clear, Secure, and Liquid Removal. Knowing these steps can enable the user to troubleshoot or improve the performance.
This initial phase in this cycle is the Compressing Phase. During this step, the last residual pressure that keeps the filter cloths in is compressed removed using compressed gas. This process is crucial to forming a gap and the cloth material and the structure, making them more efficient to clear this press and remove the formation. Once the compress phase is completed, the press is in the Open Location.
During the Clear step, the cake is removed from the filter material, or the material are maintained to prevent any remaining formation and other impurities that interfering the filtration procedure. The phase usually involves the use of physical or fluid streams for release the formation off the material. The cloth cloths are also examined for any wear or wear, and repair is performed if required to guarantee optimal performance.
This third phase of the cycle is the Secure Step. While this phase, the filter material are secured and the machine is sealed. This action involves feeding the cloth cloths in the frame, or securing them in position. The cloth cloths are also positioned to avoid any misalignment while the filtration procedure.
The final phase of this cycle is the Filtrate Discharge Phase. While the step, the pump is operated to transfer the solution to the press press, while the solution overflows through the permeate channel, creating a low-pressure environment that draws the liquid through the filter medium. The solids are retained in the frame, and the liquid is discharged as filtrate.
Knowing the varied steps of this filter cycle and conducting routine maintenance and checks can optimize machine performance, reduce downtime, and ensure compliance with regulatory standards. In addition, investing in equipment that is designed to simplify the process, such as self-cleaning filter press plate and frame cloths, or automation systems can increase the efficiency of the Filter Press.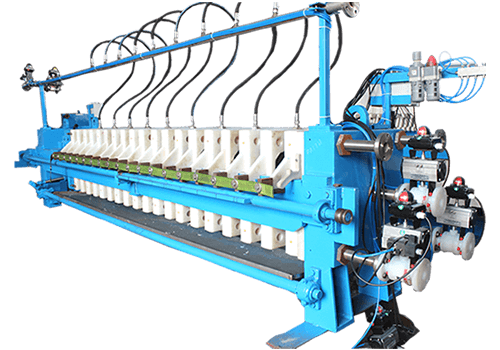
The procedure of the Filter can be divided into four primary phases: Blow, Clear, Secure, and Liquid Removal. Knowing these steps can enable the user to troubleshoot or improve the performance.
This initial phase in this cycle is the Compressing Phase. During this step, the last residual pressure that keeps the filter cloths in is compressed removed using compressed gas. This process is crucial to forming a gap and the cloth material and the structure, making them more efficient to clear this press and remove the formation. Once the compress phase is completed, the press is in the Open Location.
During the Clear step, the cake is removed from the filter material, or the material are maintained to prevent any remaining formation and other impurities that interfering the filtration procedure. The phase usually involves the use of physical or fluid streams for release the formation off the material. The cloth cloths are also examined for any wear or wear, and repair is performed if required to guarantee optimal performance.
This third phase of the cycle is the Secure Step. While this phase, the filter material are secured and the machine is sealed. This action involves feeding the cloth cloths in the frame, or securing them in position. The cloth cloths are also positioned to avoid any misalignment while the filtration procedure.
The final phase of this cycle is the Filtrate Discharge Phase. While the step, the pump is operated to transfer the solution to the press press, while the solution overflows through the permeate channel, creating a low-pressure environment that draws the liquid through the filter medium. The solids are retained in the frame, and the liquid is discharged as filtrate.
Knowing the varied steps of this filter cycle and conducting routine maintenance and checks can optimize machine performance, reduce downtime, and ensure compliance with regulatory standards. In addition, investing in equipment that is designed to simplify the process, such as self-cleaning filter press plate and frame cloths, or automation systems can increase the efficiency of the Filter Press.
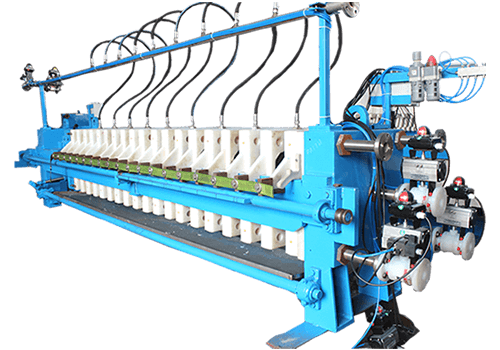
댓글목록
등록된 댓글이 없습니다.