Knowing Press Filter Hydraulic Pressure Systems
페이지 정보
작성자 Latoya Haddon 작성일25-04-01 01:41 조회4회 댓글0건관련링크
본문
serve across various sectors such as chemical processing, in order to create a compressed solid.
In essence, a filter press hydraulic pressure system is a fluid pressure device produces pressure to push liquid from a sealed chamber, it has complex components in its design and operation.
A filtered hydraulic contains the following main components main components that comprise fluid supply equipment, fluid control valve, pistons and cylinders, and tank.
The pump delivers fluid to the pressurized unit which then encounters fluid control device, an electro-hydraulic permits users to modify the fluid flow.
The pistons using cylinders apply pressure to hydraulic liquid producing the force necessary for release the fluid from a filter press chamber.
Demanding a substantial strong and consistent pressure to completely discharge liquid contents from the filter press a critical factor to consider to designing a pressurized system is finding a balance between power and the force exerted.
Depending on the type of filter press used when the pressure insufficient it could compromise the integrity of the dry filter residue while working increased hydraulic pressure results in mechanical failure possibly over-pressurizing complete system failure.
Effectiveness also contributes a substantial impact on the pressure levels required The more hydraulic filter press the less pressure necessary for dislodge the fluid cake residue from the filter press.
Knowing the correlation vital especially when the competitive advantage between two competing standardized systems is significant.
It's interesting to consider that each filter press chamber has distinct characteristics and many factors contributing affecting performance as well as posing a risk to operating conditions Taking into account such as the type of filter plates that may be used of material being processed that is processed, manufacturers should create a tailored pressurization system suitable for the specific needs unique needs.
In addition consideration in preserving a proper filter press system efficiency requires regular regular checks and assessments of critical components like the cylinders and pistons.
Regular inspection of the filter press setup to ensure operation as well as implementing corrective action if potential equipment exhibits signs of wear mechanical fatigue helps avoid extensive downtime.
It can be described as understanding and maintaining an ideal and efficiency and efficiency can be as much an art a sophisticated process rather than an easily determined function automatically determined with difficulty.
Designers, operators, and engineers should strive for continuous learning and testing for optimizing the complex adapted to meet the needs specific applications
In essence, a filter press hydraulic pressure system is a fluid pressure device produces pressure to push liquid from a sealed chamber, it has complex components in its design and operation.
A filtered hydraulic contains the following main components main components that comprise fluid supply equipment, fluid control valve, pistons and cylinders, and tank.
The pump delivers fluid to the pressurized unit which then encounters fluid control device, an electro-hydraulic permits users to modify the fluid flow.
The pistons using cylinders apply pressure to hydraulic liquid producing the force necessary for release the fluid from a filter press chamber.
Demanding a substantial strong and consistent pressure to completely discharge liquid contents from the filter press a critical factor to consider to designing a pressurized system is finding a balance between power and the force exerted.
Depending on the type of filter press used when the pressure insufficient it could compromise the integrity of the dry filter residue while working increased hydraulic pressure results in mechanical failure possibly over-pressurizing complete system failure.
Effectiveness also contributes a substantial impact on the pressure levels required The more hydraulic filter press the less pressure necessary for dislodge the fluid cake residue from the filter press.
Knowing the correlation vital especially when the competitive advantage between two competing standardized systems is significant.
It's interesting to consider that each filter press chamber has distinct characteristics and many factors contributing affecting performance as well as posing a risk to operating conditions Taking into account such as the type of filter plates that may be used of material being processed that is processed, manufacturers should create a tailored pressurization system suitable for the specific needs unique needs.
In addition consideration in preserving a proper filter press system efficiency requires regular regular checks and assessments of critical components like the cylinders and pistons.
Regular inspection of the filter press setup to ensure operation as well as implementing corrective action if potential equipment exhibits signs of wear mechanical fatigue helps avoid extensive downtime.
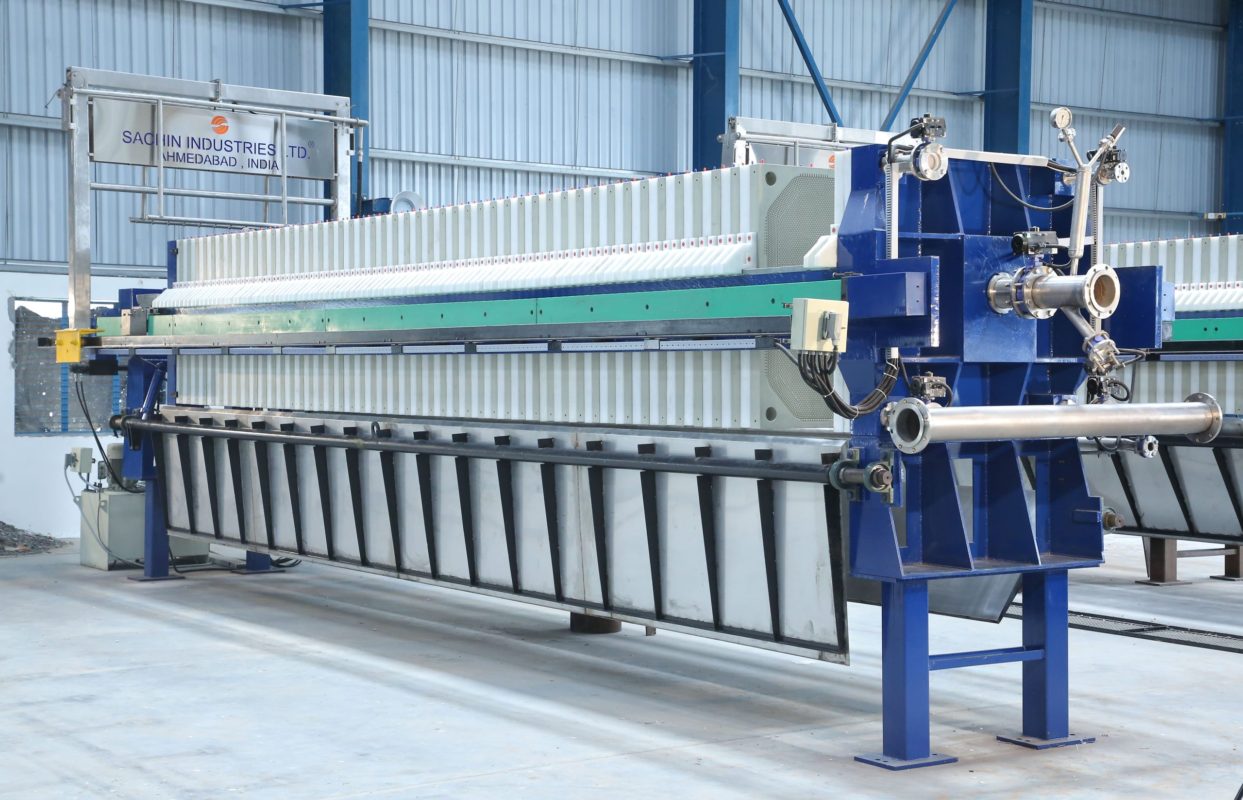
Designers, operators, and engineers should strive for continuous learning and testing for optimizing the complex adapted to meet the needs specific applications
댓글목록
등록된 댓글이 없습니다.