Maximizing Safety with Effective Calibration of Industrial Scales
페이지 정보
작성자 Princess Cadman 작성일25-03-28 18:31 조회13회 댓글0건관련링크
본문
As industries continue and grow their activities, ensuring; guaranteeing the reliability and dependability of weighing instruments is crucial for keeping quality control, minimizing waste, and avoiding costly errors. Commercial scales are a essential component in various industries such as manufacturing, logistics, and pharmaceuticals, where exact measurements are minimal.
A key; The main factor in maintaining the efficiency of industrial scales is through periodic; frequent calibration. In this article, we'll explore the significance of calibration and give guidance on optimizing safety with effective calibration of industrial scales.
Regular calibration of industrial scales is minimal to ensure accurate measurements and to prevent equipment failure. A poorly calibrated scale may generate inaccurate readings, which may compromise item quality, waste resources, and cause to costly errors. Furthermore; Additionally, inaccurate readings may also damage the credibility of a company if the issue is not addressed promptly. It is, therefore, crucial to incorporate calibration into the maintenance routine of commercial scales.
When it comes to calibration, some factors must be considered, including the type of scale being used, the extent of weights and measurements being handled, and the industry compliance needs. Different types of scales, such load cell and strain gauge, require unique calibration procedures to ensure accuracy. Furthermore, compliance with industry standards and regulations also plays a significant role in guaranteeing the calibration meets the required standards.
An effective calibration process of industrial scales involves several important steps. Firstly; Initially, the scale must be placed on a firm and firm surface to prevent movement or vibration during calibration. Then, the calibration weights or standards should be applied to the scale according to the manufacturer's instructions. After that, the readings from the scale should be evaluated to the expected values. If discrepancies are identified, the scale must be recalibrated until accurate readings are achieved.
In order to maximize safety with calibration of commercial scales, compliance to manufacturer instructions and local regulations is minimal. Additionally, operators should follow a documented procedure for calibration and take the necessary precautions to prevent damage to the equipment or personal injury during the calibration process. Regular training and education on calibration are also vital to guarantee that operators are prepared with the necessary knowledge and skills to execute effective and accurate calibration.
Lastly; Finally, монтаж автомобильных весов after the calibration is complete, it is minimal to document the results and maintain a record of the scale's performance and maintenance activities. This will enable supervisors and quality control personnel to assess the effectiveness of the calibration process and determine areas for improvement.
In conclusion, effective calibration of commercial scales is minimal for maintaining accurate measurements, avoiding equipment failure, and guaranteeing compliance with industry standards and regulations. Since following the guidelines outlined above, organizations can ensure that their commercial scales are calibrated safely and effectively, and thereby assist to keeping workplace safety, item quality, and customer satisfaction.
A key; The main factor in maintaining the efficiency of industrial scales is through periodic; frequent calibration. In this article, we'll explore the significance of calibration and give guidance on optimizing safety with effective calibration of industrial scales.
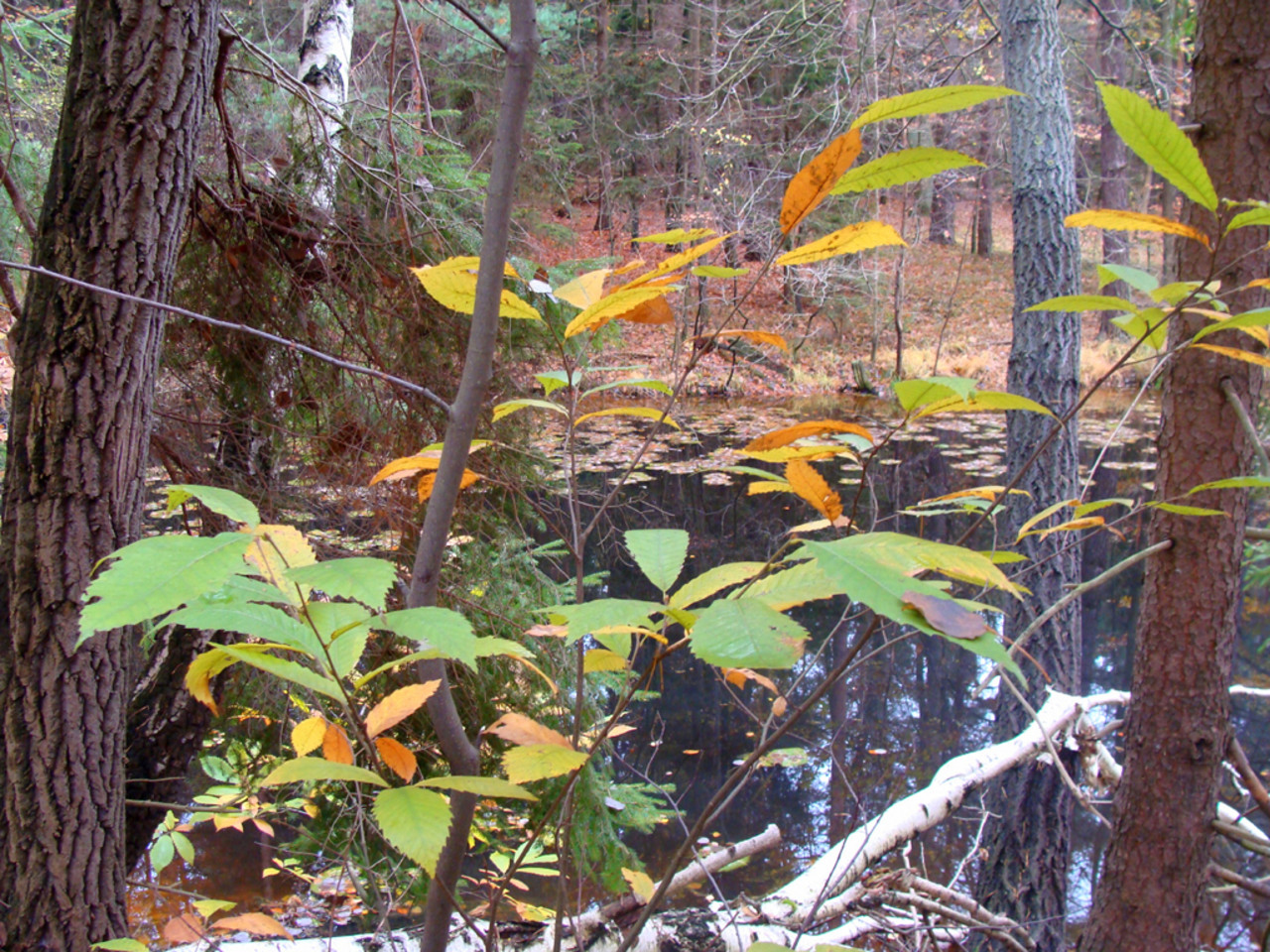
When it comes to calibration, some factors must be considered, including the type of scale being used, the extent of weights and measurements being handled, and the industry compliance needs. Different types of scales, such load cell and strain gauge, require unique calibration procedures to ensure accuracy. Furthermore, compliance with industry standards and regulations also plays a significant role in guaranteeing the calibration meets the required standards.
An effective calibration process of industrial scales involves several important steps. Firstly; Initially, the scale must be placed on a firm and firm surface to prevent movement or vibration during calibration. Then, the calibration weights or standards should be applied to the scale according to the manufacturer's instructions. After that, the readings from the scale should be evaluated to the expected values. If discrepancies are identified, the scale must be recalibrated until accurate readings are achieved.
In order to maximize safety with calibration of commercial scales, compliance to manufacturer instructions and local regulations is minimal. Additionally, operators should follow a documented procedure for calibration and take the necessary precautions to prevent damage to the equipment or personal injury during the calibration process. Regular training and education on calibration are also vital to guarantee that operators are prepared with the necessary knowledge and skills to execute effective and accurate calibration.
Lastly; Finally, монтаж автомобильных весов after the calibration is complete, it is minimal to document the results and maintain a record of the scale's performance and maintenance activities. This will enable supervisors and quality control personnel to assess the effectiveness of the calibration process and determine areas for improvement.
In conclusion, effective calibration of commercial scales is minimal for maintaining accurate measurements, avoiding equipment failure, and guaranteeing compliance with industry standards and regulations. Since following the guidelines outlined above, organizations can ensure that their commercial scales are calibrated safely and effectively, and thereby assist to keeping workplace safety, item quality, and customer satisfaction.
댓글목록
등록된 댓글이 없습니다.